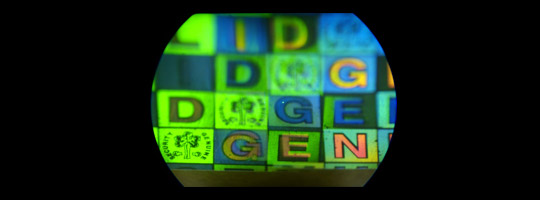
Behind the curtain…
It takes a big deal of engineering research and obstinacy to understand how the optical marvels in the surrounding nature work. Look for example to the deep iridescent blue wings of the morpho butterfly. The mystery behind this phenomenon puzzled scientists for centuries till someone discovered that the wings are colorless and that microstructures cover them that interact with incident light to create this impressive blue color.
Once the mysteries are understood, theorized and conceptualized, it opens the door to brand new optical security features, call them DOVID’s, Alphagram’s, DID’s … But understanding how it works and being able to reproduce an optical effect in a laboratory, does not mean being able to manufacture it in large quantities and repeatedly with a decent yield, in a production environment.
Manufacturing DOVID’s requires the mastery of very different technologies and techniques, some being traditional and some others being leading-edge. So, what does it take to build one of these optical security features?
1. Conversion of a 2D graphic design representative of the selected security elements, into 3D nano and/or micro-structures etched on the surface of a photoresist. Using interferential microlithography and digital holography techniques, the first element of the production chain is created, i.e. a master shim.
2. Duplication of the master shim into production worthy embossing or casting plates typically created using an electroforming process. The accuracy of the replication, the absence of artifacts and defects, and the uniformity of the deposited metal are of crucial importance to the reminder of the process.
3. Replication of the optical structures from the plates to the selected foil. Thermomechanical embossing or UV casting are typical methods used for this step. They require a strict control of the processing parameters and of the foil structure to ensure the visual aspect and functionality of the optical elements is achieved.
4. Thin film deposition over the foil surface using either metal or dielectric elements depending on the desired effect. Inspired from the chemical vapor deposition and evaporation techniques used in the electronic industry, the deposited thin film actively participates in achieving the targeted characteristics for the reflective layer of the product.
5. Selective etching of the metallic thin film. Here also inspired by technologies commonly used in the electronic domain, the goal is to selectively remove on registered locations the deposited metal so as to create a specific pattern. Using positive or negative varnishes, areas to be protected or removed are masked then submitted to a wet etch to dissolve the undesired metal.
6. Adhesive structure coating. Use of the security element on its final application relies on its capability to be deposited on its final substrate (passport page, banknote, packaging, car windshield…). The foil is therefore coated with an adhesive structure specifically formulated to withstand the mechanical and chemical constraints and requirements applicable to the application it will be used in.
7. Transformation of the manufactured foil into the format suitable for the customer. Through slitting then lamination where needed, the optical laminates over the foil, are converted into their final delivery form.
Mastering the technologies sustaining the manufacturing process is a definite must have and as a pioneer in holography, SURYS has developed a unique set of competences in optical sciences and production processes to bring to life the most complex features.
But, technology is not all. Ensuring the delivered products meet the highest quality standards, that health, safety and environmental risks are anticipated and managed, and that security infrastructure meets the market needs and customer expectations, must also be a key focus of any manufacturing operation. A focus that SURYS has always kept in mind and that translates into the certifications the company holds: ISO 9001:2008 for the Quality System; ISO 14001:2004 and OHSAS 18001:2007 for the Health, Safety and Environmental aspects; ISO 14298:2013 Government class for security.
José Lopez